ZHN
Nanoindenter, Härteprüfer und mehr
Der Universelle Nanomechanische Tester ZHN
Der Universelle Nanomechanische Tester ZHN ist eine Weiterentwicklung der bewährten Technik von ASMEC die unter dem Namen UNAT verkauft wurde.
Durch seine hohe Modularität ist er ist mehr als ein Nanoindenter oder Härteprüfer. Je nach Ausbaustufe kann er genutzt werden
Mit einem Messkopf als:
- Nanoindenter / Härteprüfer für Messungen zwischen 0,02 mN − 20000 mN
- Mikro−Zugprüfgerät im selben Kraftbereich
- Ermüdungstester bis 2 Hz quasistatisch oder bis 300 Hz mit Dynamikmodul
- Dynamisch Mechanischer Tester (DMA) bis etwa 100 Hz mit Dynamikmodul
- Profilometer und mit Dynamikmodul auch Stiffness/Modulus−Mapping
- Scratchtester ohne Messung der Reibkraft
Mit einem zweiten Messkopf für laterale Kraft−Verschiebungs−Kurven als:
- Scratchtester mit Messung der Reibkraft
- Oszillierender Scratchtester (Schwingung der Probe senkrecht zur Scratchrichtung)
- Mikro−Verschleißtester für reversierenden Verschleiß
- Mikro−Fretting−Tester (laterale Oszillationen) mit Dynamikmodul
- Messgerät für die laterale elastische Deformation. Daraus können abgeleitet werden
- Laterale Kontaktsteife
- Poissonzahl (neu)
- Eigenspannungen unter Nutzung der FilmDoctor Software (neu)
- Laterale Versagensmechanismen
Besondere Merkmale des Gerätes, die es von anderen Geräten auszeichnen:
- Sehr hohes Signal−zu−Rausch−Verhältnis von etwa 106 : 1, so dass auch bei Messungen mit 2 N Messkopf eine ausgezeichnete Auflösung erreicht wird.
Mehr
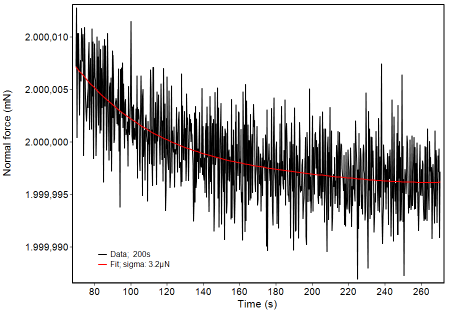
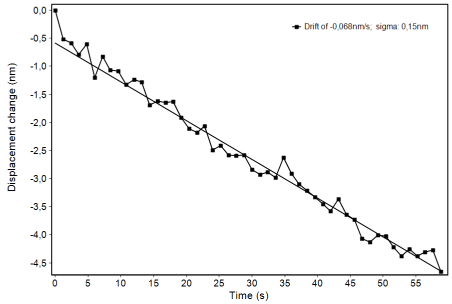
Das Spannungssignal der induktiven Sensoren (LVDTs) des ZHN wird mit AD-Wandlern mit einer Auflösung von 24 Bit und einer Frequenz von 156 kHz aufgezeichnet. Die effektive digitale Auflösung einer maximal genutzten Frequenz von 10 kHz beträgt 28 bit. Dies entspricht bei der Wegmessung einer Auflösung von besser als 0,002 nm.
Die Standardabweichung des Signalrauschens beträgt bei der Wegmessung für eine Datenrate von 16 Hz typisch weniger als 0,3 nm bei der Wegmessung und weniger als 3 µN bei der Kraftmessung für den 2 N Messkopf. Dies ist das Beste was bisher für diesen Sensortyp erreicht wird. Bei geringeren Abtastraten reduziert sich das Rauschen weiter. Am Ende der Messbereiche ist das Rauschen etwas größer.
Der großen Vorteile der LVDTs gegenüber kapazitiven Sensoren bestehen in dem größeren Messbereich von bis zu 1 mm (bei dem eingesetzten Sensortyp) und dem deutlich besseren Überlastungsschutz. Da es keinen Anschlag gibt, wie bei kapazitiven Sensoren, kann der Sensor bei einer Überlastung nicht zerstört werden. Dies macht die ZHN Messköpfe so robust.
Abb.1 zeigt das Signalrauschen bei Maximalkraft von 2 N über einen Zeitraum von 200 s. Im Gegensatz zu den meisten anderen Geräten wird das Kraftsignal über einen eigenen Sensor separat gemessen, unabhängig vom Spannungs- oder Stromsignal des Aktors. Die Standardabweichung der Differenz zur Fitkurve (rot) beträgt 3,2 µN. Die leichte Krümmung der Kurve entsteht durch die Wirkung der Regelung, die bei kleinen Differenzen zum Sollwert sehr schwach ist.
Abb.2 zeigt die Änderung des Wegsignals während einer Haltezeit von einer Minute zur Bestimmung der thermischen Drift. Bei einer geringeren Datenrate beträgt die Standardabweichung des Wegrauschens nur 0,15 nm. Die thermische Drift lag bei -0,068 nm/s.
- Äußerst robuster Messkopf mit großer Toleranz gegen Überlastung durch Nutzung induktiver Wegsensoren ohne Anschlag und ein steifes Federsystem. Dies ermöglicht:
- Einen sehr schnellen Spitzenwechsel ohne zusätzliche Schutzmaßnahmen
- Die Verwendung von beliebigen Prüfkörpern und Adaptern mit dem bis zu 10−fachen Gewicht der Diamantspitzen
Mehr
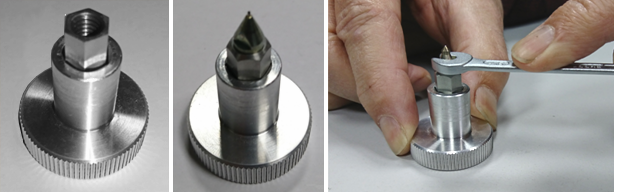
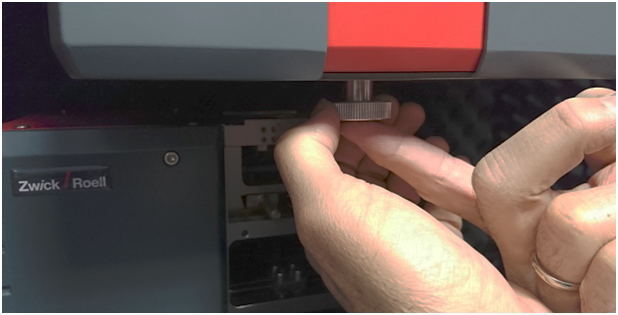
Die Spitze wird zusammen mit einem Adapter aus dem Messkopf geschraubt. Die Spitze sitzt dabei geschützt im Werkzeug aus Aluminium (links). Anschließend wird sie zusammen mit dem Adapter im Werkzeug umgedreht (Mitte) und mit einem normalen Schraubenschlüssel vom Adapter abgeschraubt (rechts). Genauso wird eine neue Spitze installiert.
Zum Schluss wird die neue Spitze mit Adapter wieder in den Messkopf eingeschraubt (unten). Dazu ist keine zusätzliche Sicherung im Messkopf nötig, da das Federsystem im Messkopf steif genug ist, um der Fingerkraft standzuhalten. Für erfahrene Nutzer dauert ein Spitzenwechsel weniger als 3 Minuten. Anschließend kann der Abstand Indenter-Kamera mit einer Software Routine ebenfalls in weniger als 3 Minuten kalibriert werden.
Beim ZHN ist es nicht ungewöhnlich, dass die Prüfspitze für verschiedene Messungen fünfmal am Tag gewechselt wird.
- Einfach zu montierende Schaftverlängerungen erlauben Messungen in Vertiefungen oder Flüssigkeiten
Mehr
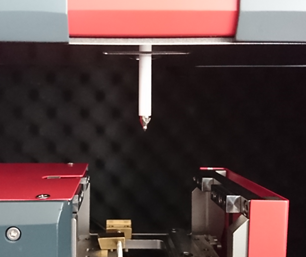
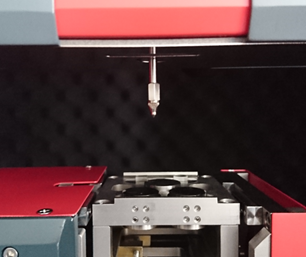
Beispiele für Schaftverlängerungen.
Links eine Verlängerung aus Macor Glaskeramik, die vorrangig zusammen mit dem Probenheizer verwendet wird,
rechts eine Verlängerung aus Stahl mit der Messungen in Vertiefungen oder Löchern durchgeführt werden können. Ebenso sind Messungen in Flüssigkeiten möglich.
Durch den Nutzer können auch eigene Schaftverlängerungen entworfen und genutzt werden, da der Messkopf trotz des Zusatzgewichts seinen Messbereich beibehält.
- Gleiche Funktionsweise in Druck− und Zugrichtung. Dadurch kann das Gerät auch als Mikro−Zugprüfer verwendet werden
- Sehr steife Rahmenkonstruktion bei der die Indenterachse direkt unter der Bewegungsachse der Höhenverstellung sitzt. Dadurch gibt es kein Kippmoment beim Aufbringen der Kraft.
- Modularer Aufbau bei dem Messköpfe für verschiedene Kraftbereiche (0,2 N; 2 N; 20 N) durch den Nutzer selbst ohne Schwierigkeiten ausgetauscht werden können unter Verwendung der gleichen Steckverbinder.
- Die einzigartige und patentierte Lateralkrafteinheit erlaubt sehr präzise Messungen lateraler Kraft−Verschiebungs−Kurven, die mit keinem anderen Gerät möglich sind. So können laterale Steifigkeiten oder Stick−Slip Effekte bei Reibversuchen und vieles mehr untersucht werden. Durch die Kombination der zwei Messkopfe können Belastungen, die in Anwendungen auftreten, wesentlich besser im Labor simuliert werden.
Mehr
Die Lateralkrafteinheit (LFU) ist ein zweiter völlig unabhängiger Messkopf mit dem zusätzlich zur senkrechten Belastung der Probenoberfläche auch Belastungen in lateraler Richtung simuliert werden können, wie sie in Anwendungen häufig auftreten. Insbesondere in Kombination mit Spannungsrechnungen kann dadurch die Entstehung von Fehlern in Oberflächen besser nachvollzogen werden. Die Wegauflösung ist genauso gut, wie in normaler Richtung. Die Kraftauflösung ist etwas schlechter, da die Federkraft von steifen Haltefedern berücksichtigt werden muss.
Das patentierte Prinzip das LFU ist in Abb. 1 erläutert. Der Probenhalter sitzt auf einer Halteplatte, die an der Mitte von vier senkrechten Blattfedern befestigt ist. Diese Konstruktion ist sehr steif in senkrechter Richtung, so dass sich keine merkliche Verschlechterung der Gerätesteife ergibt. Bei der seitlichen Auslenkung durch ein Piezoelement von maximal ± 70 µm gibt es keine Höhenveränderung der Probe. Beide Bewegungen (normal und lateral) sind damit komplett entkoppelt. Die durch das Piezoelement aufgebrachte Gesamtkraft wird über ein Federsystem unabhängig gemessen, wobei die Auslenkung der Federn durch einen induktiven Wegsensor (LVDT) ohne Anschlag bestimmt wird. Eine Klampe, die durch einen kleinen Motor geschlossen oder geblockt wird, ermöglicht im geschlossenen Zustand die Kraftübertragung. Im geblockten Zustand verhindert sie, dass sich der Probenhalter mit der Probe seitlich bewegen kann, wie es für reine Härtemessungen erforderlich ist.
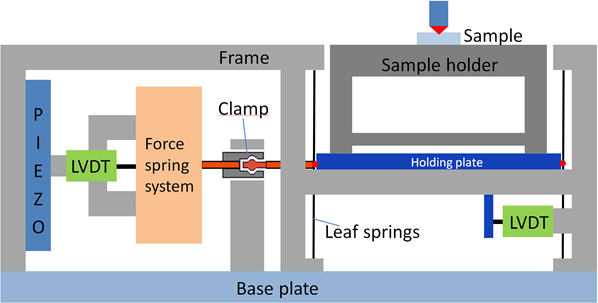
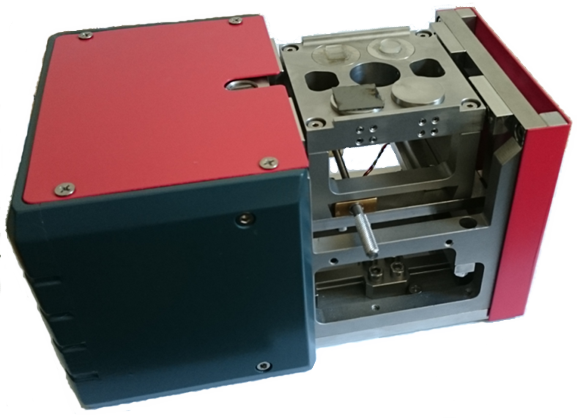
Durch dieses Prinzip kann (im Gegensatz zu Scratchtestern und anderen Geräten) eine Kraft aufgewendet und gemessen werden, auch ohne dass eine seitliche Bewegung stattfindet. Dies ist z. B. der Fall, wenn der Prüfkörper auf der Probenoberfläche haftet. Der Übergang von Haft- zu Gleitreibung kann genau bestimmt werden. Zur Bestimmung der Reibungskraft auf der Probe ist von der gemessenen Gesamtkraft die Federkraft der Haltefedern abzuziehen. Die genaue Federkonstante wird daher vor Beginn einer Messserie durch eine Messung gegen Luft ohne Kontakt der Spitze mit der Probe bestimmt und anschließend korrigiert (Abb. 3 und 4). Die hohe Auflösung der Messung erlaubt die Bestimmung der elastischen Verformung im Kontakt von teilweise weniger als 10nm und damit die Bestimmung der lateralen Kontaktsteife.
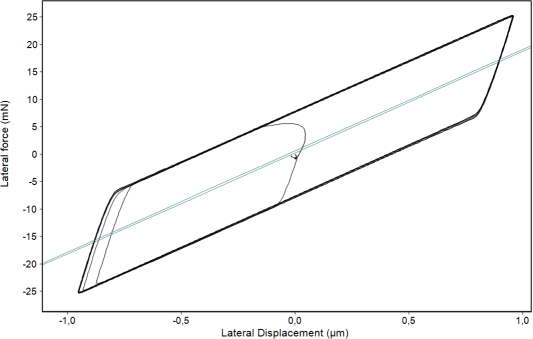
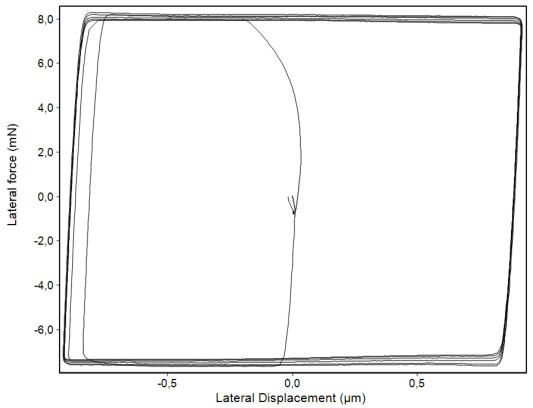
Die Kombination beider Messköpfe erlaubt eine Vielzahl von neuartigen Messmethoden von denen hier nur eine beispielhaft dargestellt werden kann. Sie ist in den Abbildungen 6 und 7 erläutert.
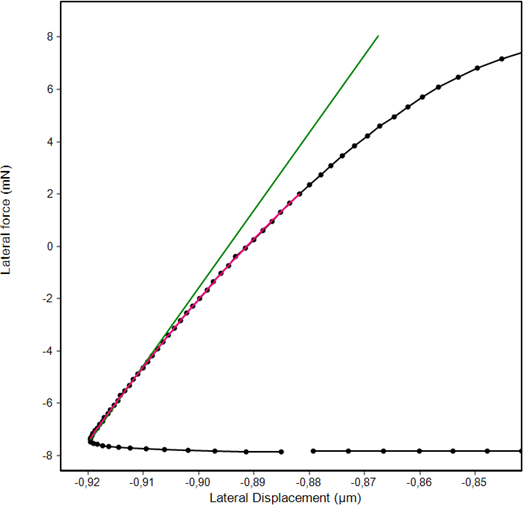
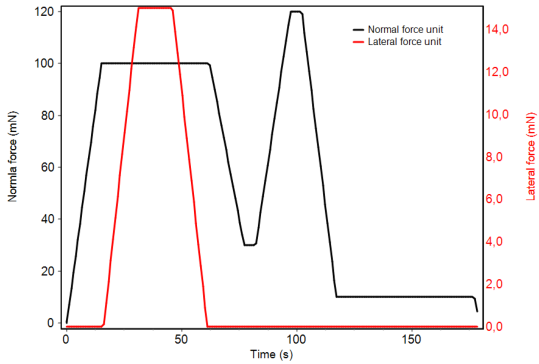
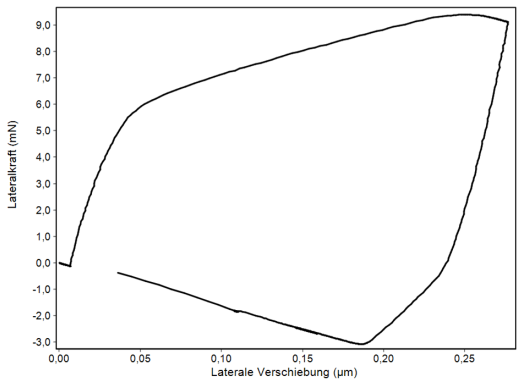
Abb. 7:
Zu Abb. 6 gehörige laterale Kraft-Verschiebungs-Kurve eines Berkovich Indenters in Quarzglas. Nachdem durch die Normalkraft ein plastischer Eindruck erzeugt wurde, wird der Eindringkörper seitlich gegen die Wände des Eindrucks gedrückt. Dabei gibt es zunächst bis etwa 5 mN rein elastische Deformation bevor sich die Probe auch seitlich plastisch um etwa 200 nm verformt. Aus der ebenfalls zunächst rein elastischen Verformung bei der Entlastung am rechten Teil der Kurve lässt sich mit einem entsprechenden (recht komplexen) Modell die Poissonzahl berechnen. Außerdem können die Fließgrenze des Materials und teilweise Eigenspannungen abgeleitet werden. Die dafür notwendigen Berechnungen sind nicht Bestandteil der InspectorX Software sondern erfordern eine zusätzliche externe Software.
- Serienmäßiger Probenhalter mit 5 Plätzen für verschieden hohe Proben und einem Anschluss zur Messung des Kontaktwiderstands zwischen Spitze und Probe (bei Verwendung von leitfähigem Diamant oder anderen Indentermaterialien)
Mehr
Standard-Probenhalter für bis zu 5 verschieden hohe Proben
- 5 unmagnetische Stahlzylinder zur Probenbefestigung, Durchmesser 24 mm, Höhe 14 mm
- Die Proben werden mit Hartwachs aufgeklebt
- Ausgleich unterschiedlicher Probenhöhen bis etwa 8 mm
- Wenn möglich Justierung der Probenoberfläche an der obersten Kante des Halters
- Isolierte Oberseite zur Messung des Kontaktwiderstandes Spitze – Probe
Weitere Informationen zu den ZHN Probenhaltern finden Sie hier: Probenhalter für das ZHN
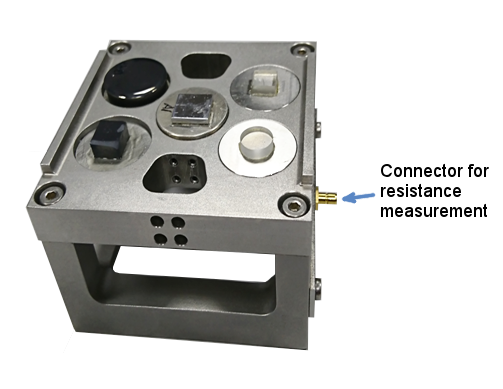
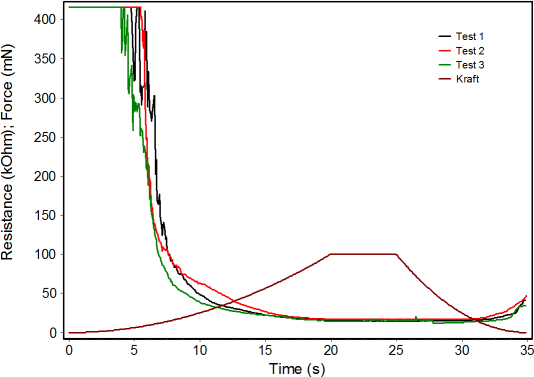
- Sehr großer Verfahrweg von 70 mm in Z−Richtung, so dass auch sehr hohe Proben vermessen werden können. Ohne den zweiten Messkopf (LFU) lassen sich auch große Proben mit über 20 cm Höhe und 50 cm Länge adaptieren. Der große Bauraum lässt genug Platz für Zusatzeinrichtungen.
- Einzigartige Optik mit sehr hoher Vergrößerung bis 3250−fach (76 nm pro Pixel) und der Verwendung von zwei Kameras für verschiedene Vergrößerungen, so dass die Vergrößerung ohne Drehen eines Objektivrevolvers bei hoher Positionstreue umgeschaltet werden kann.
- Spezielles Tip Check Modul für den täglichen Test des Gerätezustands beispielsweise innerhalb eines Qualitätssicherungssystems. Es nutzt eine permanent installierte Quarzglasprobe an einem separaten Ort so dass keine Probe gewechselt werden muss. Die Software vermerkt in einer Datenbank wo bereits Messungen durchgeführt wurden.
Mehr
Das Tip Check Modul des ZHN erlaub eine automatisierte Kontrolle und Dokumentation des Gerätezustands und des Zustands des Eindringkörpers. Dazu ist eine Quarzglasprobe on einem festen zusätzlichen Probenhalter installiert, so dass keine Probe gewechselt werden muss. Die Abbildung zeigt dies für die LFU, jedoch auch ohne LFU gibt es diesen zusätzlichen Halter. Da die Probe sich immer am selben Ort befindet kann durch die Software vermerkt werden, wo bereits Messungen durchgeführt wurden. Auf eine 8 x 8 mm² Probe passen über 5000 Eindrücke in einem Abstand von 100 µm oder 20.000 Eindrücke in einem Abstand von 50µm. Freie Messstellen werden durch grüne Punkte markiert, genutzte durch rote Punkte (s. Abbildung).
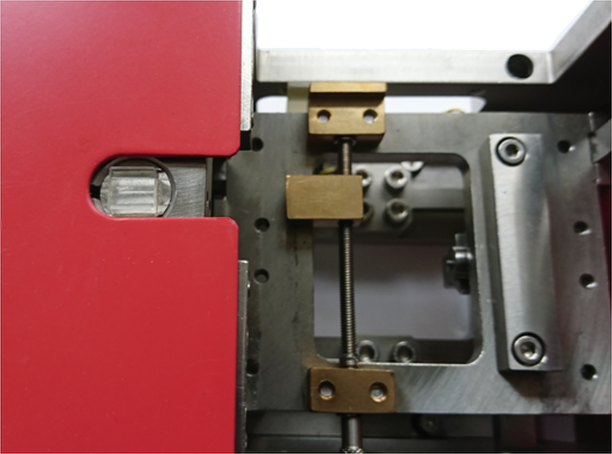
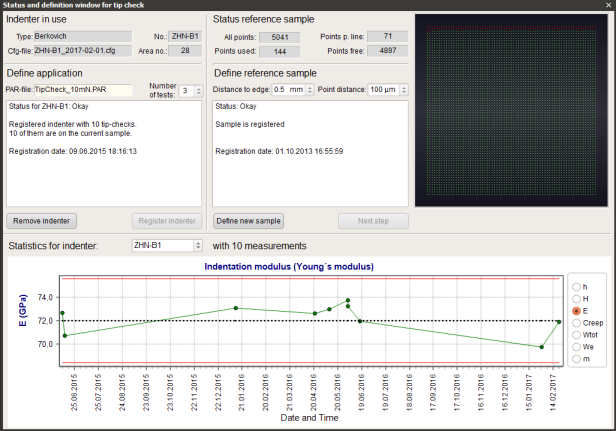
Für jeden Eindringkörper wird ein Messablauf (Application) und die Zahl der Messungen definiert, mit denen der Gerätezustand geprüft werden soll. Üblicherweise reichen 3 Tests. Um Veränderungen des Eindringkörpers deutlich zu erkennen, werden Messungen bei kleinen Kräften, z.B. 10 mN, empfohlen.
Nach der automatischen Mittelung und Auswertung der Messungen wird kontrolliert, ob der Sollwert des E-Moduls von Quarzglas von 72 GPa innerhalb bestimmter Grenzen erreicht wird. Es lassen sich auch andere Parameter wie Härte oder Eindringtiefe prüfen. Die Ergebnisse werden in einer Grafik angezeigt und in einer (geschützten) Datenbank eingetragen.
- Äußerst präzise Routinen zur Bestimmung der Flächenfunktion oder der Radiusfunktion bei kugelförmigen Spitzen und der Funktion der Gerätesteife (es wird nicht nur ein kraftunabhängiger Wert verwendet). Als einziges Gerät lässt es die Bestimmung der Flächenfunktion mit zwei Materialien gleichzeitig zu, um eine Materialabhängigkeit auszuschließen.
Mehr
Für genaue Messungen ist es erforderlich die Flächenfunktion der Prüfspitze zu bestimmen und ihre Richtigkeit permanent zu prüfen, denn auch Diamant verschleißt mit der Zeit.
Die Norm DIN EN ISO 14577-2 Anhang C unterscheidet zwischen direktem und indirektem Kalibrierverfahren.
Bei dem direkten Verfahren wird die Prüfspitze mit einem anderen Gerät, meistens mit einem Atomkraftmikroskop (AFM), abgetastet und daraus die projizierte Fläche in Abhängigkeit vom Abstand zur äußersten Spitze ermittelt. Weil dafür ein weiteres hochgenaues Messgerät erforderlich ist, wird dieses Verfahren selten eingesetzt.
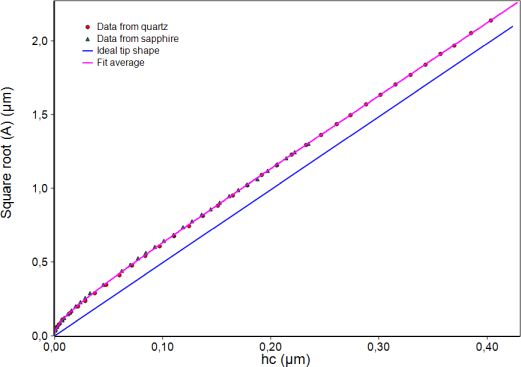
Beim indirekten Verfahren wird die projizierte Fläche anhand von Eindring-Messungen an einem Referenzmaterial mit genau bekanntem E-Modul und Poissonzahl ermittelt. Das Referenzmaterial soll außerdem eine geringe Rauheit und eine gute Homogenität haben und möglichst keinen pile-up oder sink-in Effekt aufweisen. Meist wird dafür Quarzglas verwendet.
Das Ergebnis für die Flächenfunktion darf nicht materialabhängig sein. Die einzige Möglichkeit dies zu überprüfen ist die Messung an einem weiteren Referenzmaterial mit deutlich unterschiedlichem E-Modul. Beim ZHN wird dafür Saphir Einkristall verwendet. Für beide Materialien müssen die Flächenfunktionen übereinstimmen.
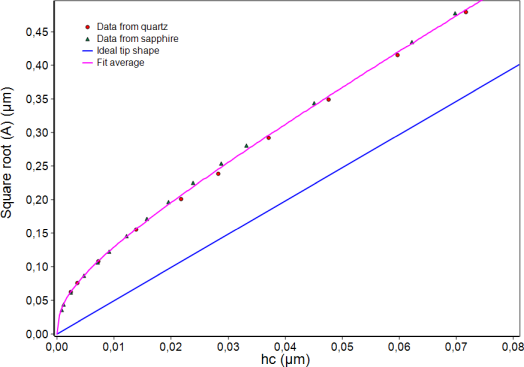
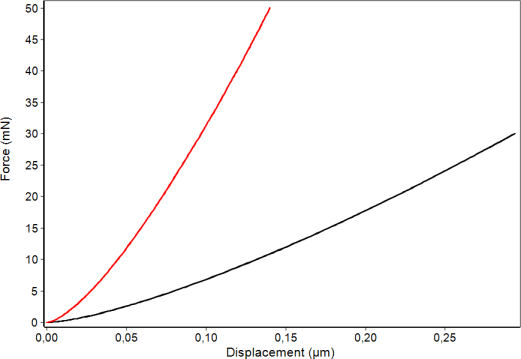
Die Software des ZHN ist als einzige Software für den Vergleich der Ergebnisse von zwei verschiedenen Referenzmaterialien vorbereitet. Dieser Vergleich erlaubt zusätzlich die Bestimmung der Gerätesteifigkeit oder -nachgiebigkeit mit derselben Prozedur. Außerdem werden radiale Verschiebungskorrektur und variabler Epsilon-Faktor standardmäßig verwendet.
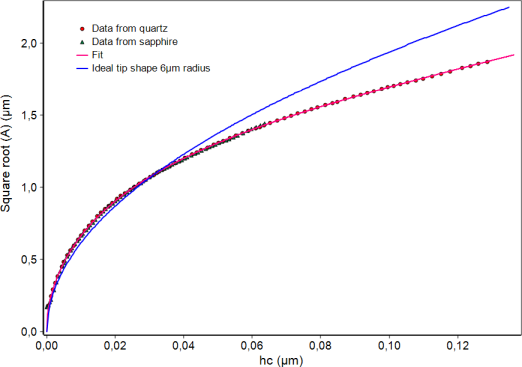
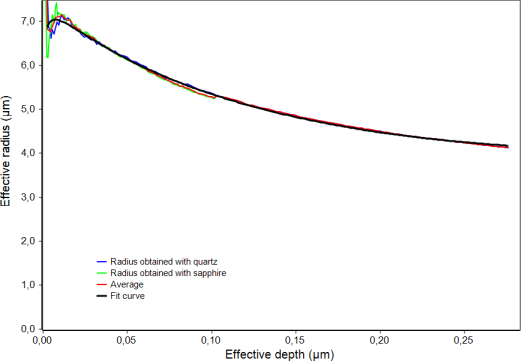
- Ein präzises optionales Dynamikmodul erlaubt die Überlagerung von Schwingungen bis 300 Hz und die Messung von Amplituden und Phasenverschiebungen. Die kontinuierliche oder quasi−kontinuierliche Messung der Kontaktsteife ermöglicht eine tiefenabhängige Bestimmung von Härte− und E−Modul schon ab Tiefen von 10 nm. Einzigartig ist der große Amplitudenbereich bis über 50 mN so dass das Gerät für Ermüdungstests eingesetzt werden kann.
Mehr
Bei der Methode der kontinuierlichen Steifigkeitsmessung (CSM), wie sie vor mehr als 20 Jahren von Nanoinstruments erfunden wurde, wird kontinuierlich eine kleine Schwingung auf das statische Kraftsignal überlagert (Abb. 1). Das Verhältnis aus der Kraft- und Wegamplitude ergibt nach einigen Korrekturen, die die schwingende Masse, die Frequenz und den Dämpfungskoeffizient berücksichtigen, die Kontaktsteifigkeit zwischen Prüfkörper und Probe.
Bei der CSM Methode ist die statische Kraft während der Belastung bei jeder Schwingung etwas unterschiedlich. Das erschwert die Mittelung mehrerer Schwingungen und die Regelung. Das ZHN beherrscht auch die CSM Methode.
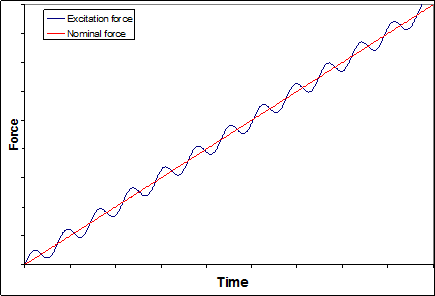
ASMEC hat eine etwas andere Methode entwickelt, die wir Quasi kontinuierliche Steifigkeitsmessung (QCSM) nennen. Dabei wird die Kraft in Stufen erhöht und nur während einer kurzen Haltezeit von etwa 0,5 s – 3 s an jeder Stufe die Schwingung eingeschaltet (Abb. 2). Dadurch können mehrere Schwingungen gemittelt werden und die Regelung wird erleichtert. Beispielsweise werden bei einer Frequenz von 40 Hz und einer Haltezeit (dwell time) von 1,4 s 56 Amplituden gemessen. Bei der QCSM Methode werden davon die ersten 20 % der Schwingungen nicht für die Mittelung berücksichtigt, um den Einfluss des Kriechens auf das Ergebnis zu reduzieren. Dies spielt insbesondere bei viskosen Materialien eine Rolle. Ein Beispiel zeigt Abb. 3. Dort sind die einzelnen Amplituden einer Kraftstufe von 1,4 s bei einer Messung mit Berkovich Indenter in Saphir zu sehen. Die Wegamplitude wurde sehr klein gewählt, um die Messung möglichst wenig zu beeinflussen und die Auflösung des Gerätes zu demonstrieren. Beim Verglich mit anderen Geräten ist zu berücksichtigen, dass beim ZHN die maximale Amplitude angegeben wird und nicht der Effektivwert. Es ergeben sich folgende Resultate:
Wegamplitude: 2,46 nm; Standardabweichung 0,22 nm; statistischer Fehler 2,8 %
Kraftamplitude 0,741 mN; Standardabweichung 0,0025 mN; statistischer Fehler: 0,1 %
Die Genauigkeit kann durch eine etwas längere Haltezeit oder eine größere Amplitude weiter verbessert werden.
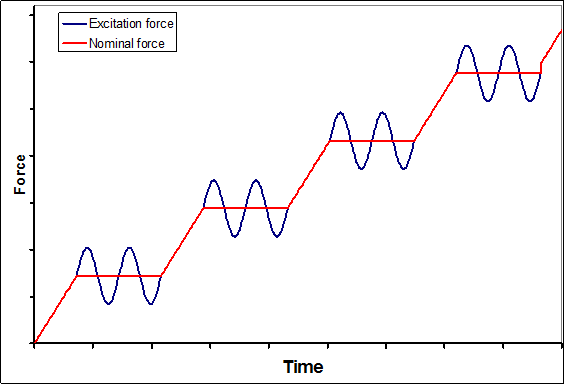
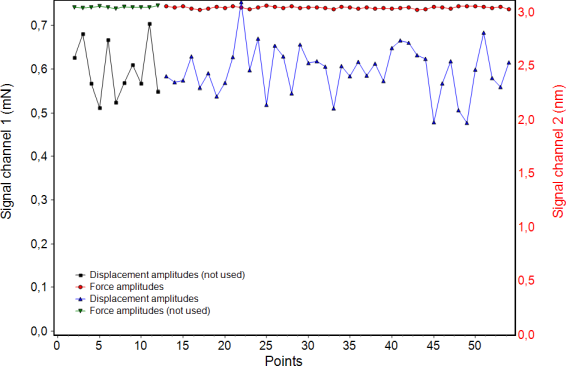
Sowohl CSM als auch QCSM Methode erlauben eine tiefenaufgelöste Messung von Härte und E-Modul an ein und derselben Stelle. Dadurch können damit wesentlich mehr Informationen gewonnen werden als mit normalen Eindruckmessungen. Die Standardeinstellung bei der QCSM Methode hat 30 Kraftstufen. Dies entspricht Messungen mit 30 verschiedenen Kräften. Außerdem ist die Genauigkeit bei sehr kleinen Kräften höher als bei Einzelmessungen. So ist es ohne Probleme möglich mit dem 2 N Messkopf genaue Werte für Kräfte von 100 µN oder 10 nm zu bekommen.
Die Ergebnisse sind bis etwa 75 Hz (je nach Material und Indenterform) unabhängig von der Frequenz. Dies wird in Abb. 4 anhand von Messungen auf Quarzglas demonstriert. Die Kurven für den tiefenabhängigen E-Modul wurden jeweils durch Mittelung aus 6 Einzelmessungen erzeugt. Der Fehlerbalken gibt den statistischen Fehler an. Ein genauer Vergleich der CSM und der QCSM Messung in Abb. 5 zeigt, dass der Fehler bei der gleichen Schwingungsfrequenz von 40 Hz bei der CSM Messung deutlich größer ist.
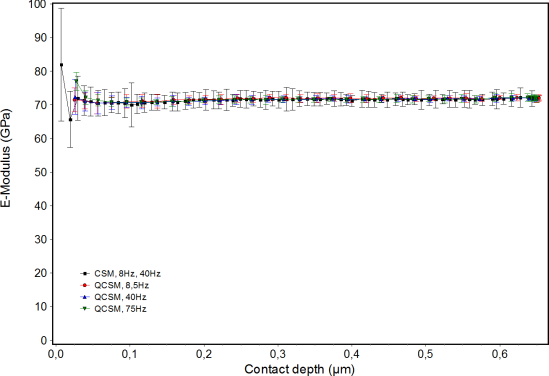
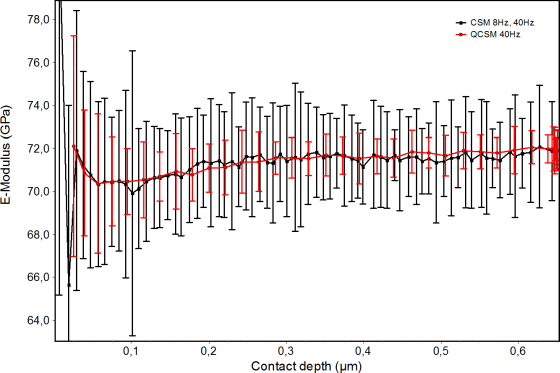
Eine separate Applikation ermöglicht einen Frequenzdurchlauf (Frequenzy sweep) zur Bestimmung des frequenzabhängigen E-Moduls von viskosen Materialien. Abb. 6 zeigt das für die Messung eines Elastomers mit dem Namen Affinity. In diesem Fall waren korrekte Messungen bis 100 Hz mit einem Kugelindenter von 7 mm Durchmesser möglich. Für diese Probe standen auch DMA Daten bis 20 Hz zur Verfügung mit denen verglichen werden kann. Angesichts der unterschiedlichen Kontaktgeometrien beim Eindruckversuch und beim DMA Test ist die Übereinstimmung sehr gut.
Eine weitere Besonderheit des ZHN ist, dass sehr große Kraftamplituden von über 50 mN bei der Schwingung erreicht werden können. Dies ermöglicht Ermüdungstests auch mit höheren Frequenzen als 75 Hz da dort keine exakten Kontaktsteifigkeiten ermittelt werden müssen.
Abb. 7 zeigt eine Schwingung des Indenters gegen Luft mit einer Frequenz von 10 Hz und einer Abtastrate von 512 Hz mit der Oscilloscope Funktion der Gerätesoftware. Es werden immer 512 Punkte im Bild dargestellt. Da die Werte durchlaufend erneuert werden, ist immer an einer Stelle der Grafik ein Sprung zu erkennen (hier bei 0,9 s), der jedoch keine Beeinträchtigung der Funktion darstellt.
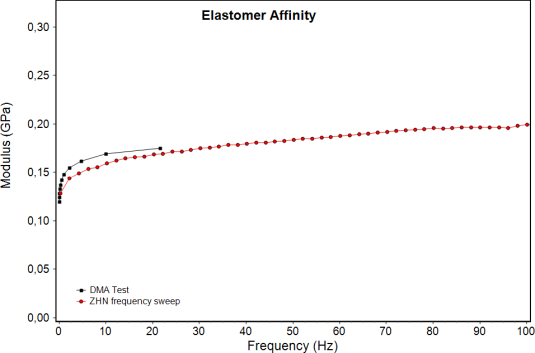
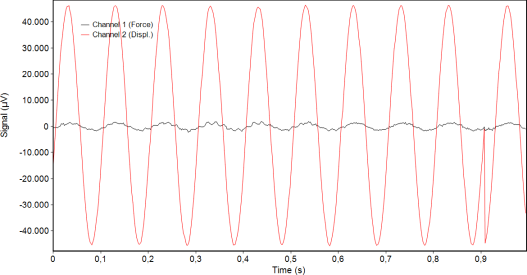
Abb. 8 zeigt das komplette Oscilloscpe Fenster bei der Maximalfrequenz von 300 Hz ebenfalls für eine Schwingung gegen Luft. In diesem Fall lag die Abtastfrequenz bei 13 kHz. Maximal sind rund 40 kHz möglich. Durch die träge Masse der bewegten Teile kann das System nicht ausreichend schnell folgen und es entsteht ein Kraftsignal, dass deutlich größer als das Wegsignal ist. Im direkten Kontakt mit einer Probe ändern sich die Amplitudenverhältnisse. Dieses Beispiel verdeutlicht schön die Unabhängigkeit von Kraftmessung und Krafterzeugung beim ZHN. Der Indenter kann frei schwingen und wird nicht durch den Aktor (den Piezo) gedämpft.
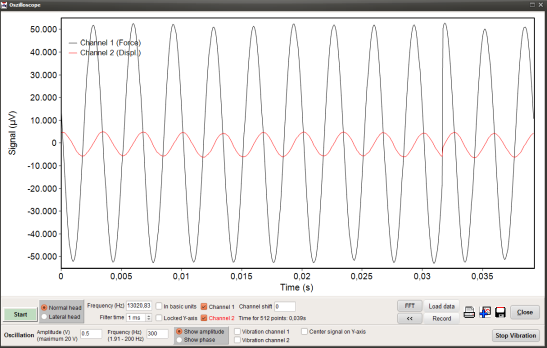
- Eine Vielzahl von Zusatzmodulen sind verfügbar wie beispielsweise
- Weißlichtinterferometer (optisches Profilometer)
- Atomkraftmikroskop (AFM)
- Probenheizer bis 400 °C
- Probenkühler bis −10 °C